10 March 2022
As if the COVID-19 pandemic wasn’t enough, the Russian invasion of Ukraine and the likelihood of further escalation has startled policy-makers and strategists into reconsidering the foundational structures of our modern supply chains. Last year’s disruption of global supply chains, thought by a few commentators to be a short-lived “storm in a teacup”, has become the headwind holding back the global recovery.
To understand why this issue is so pernicious and long-lasting, we have to look at the underlying environmental issues that allowed it to grow so quickly and become so widespread. A central plank of Donald Trump’s campaign for the US Presidency in 2016 was criticism of the export of manufacturing jobs to China through the ‘90s and early 21st Century. His trade war with China in 2018 destabilised what was by then a very sophisticated fulfilment arm of US and EU brands. The Ukraine crisis has made China nervous about its relationships with both Russia and the West. How it will react – and if it decides to seize the long-disputed territory of Taiwan, a global semiconductor manufacturing powerhouse, while NATO is distracted – will have profound implications for the West.
So, when coronavirus hit, there were already disruptions to both the supply of some key commodities and the infrastructure itself as containers clogged ports and vessels couldn’t dock. The collapse in demand during the worst of the pandemic and the subsequent surge following the reopening of most trade has been a stress test that the fine mechanisms of the old supply chain were not built to withstand. Even before the Ukraine crisis, our recovery to a pre-pandemic sized economy was not expected until late in 2022.
The MPC also expects consumer demand to be suppressed by tax rises and inflation, causing real income squeezes. For most businesses these mean higher input costs on materials combined with rising wage bills at the same time.
The underlying causes of the supply chain issue are still with us. In spite of US/China cooperation at COP26, that is still very much a fractured relationship. Whilst the supply of containers and the ships to carry them is increasing, it is a very gradual improvement in system capacity. The lack of HGV drivers around the world, but particularly in the UK post-Brexit, is forcing conversations about using rail transport as part of a future response to supply chain fragility, but it will take years to improve rail infrastructure and so it does little to mitigate today’s acute problem.
If manufacturers are to build supply chains that are both resilient and as efficient and cost effective as possible, it will take a much larger overhaul. The semiconductor issue in the automotive supply chain, for example, isn’t just a loss of capacity but a shift in technology.
Cars have many old style, low bit-rate chips in them. The chip makers have largely stopped making them and moved to higher value, high bit-rate chips. But because the car industry model is to reengineer vehicles over a multi-year cycle, the chips become obsolescent during the build period of the vehicle. This is why Tesla has created an engineering cycle that matches the chip. They know that semiconductors will be a problem forever if their processes aren’t synchronised. Others must follow.
The West must now seek to disentangle itself from strategic supply chains that rely on Russian materials, particularly precious metals, oil and gas. War is the greatest technology accelerator and the governments of NATO countries whilst busy securing short term alternative supplies of oil and gas (by reopening old fields and re-looking at fracking in the UK for example) are now acutely focused on the long-term winning strategy of energy independence from fossil fuels. If we hope to prevent climate change and decisively shift the centre of geopolitical power away from those countries prepared to use the supply of fossil fuels as a form of economic warfare, now is the time to do it. Nuclear and renewables have never been of so much interest to governments.
Placing the customer first
In 1945, another economy found itself facing acute shortages of labour and material, one that had been ravaged by war. Japan turned to what were at the time novel solutions to acute supply chain shortages by inventing Lean Manufacturing. The revolutionary Toyota Production System focused on eliminating waste, building resilient systems and using the least amounts of both labour and material.
The UK economy, in common with all advanced economies since Russia invaded Ukraine, is facing a prolonged labour shortage and supply chain disruption. Competition for material in times of conflict is immense. We would do well to revisit the lessons of Lean. Many commentators have blamed Lean practices for reducing inventory to levels that can’t be sustained in disrupted times, but this is far too simplistic a reading of the situation. Lean focuses on first meeting the expectations of the customer in quality, cost and delivery. Minimum level inventory systems have failed the global stress test and expecting them to be the right answer in future is to ignore the lessons of today.
UK businesses must now listen to the Voice of their Customers. They must revisit their Value Streams at the fundamental level and use the same ingenuity the Japanese used to overcome their supply chain dislocations, to meet their customers’ needs today. They will need to build a new system founded on resilience, energy efficiency, and value for money, not just lowest levels of inventory.
So what can manufacturers consider?
For UK manufacturers, this will mean large-scale technology integration and new applications using AI and robotics. UK productivity is only 80 per cent of Germany’s. Manufacturers will be price takers on materials and skilled labour for an extended period, and interest rates are set to rise. Practically, the only place to look for savings now are in:
- procurement through new commercial arrangements;
- throughput and yield uplifts in their own facilities; and
- end-to-end supply chain optimisation.
All of these will have large technology components, but the technology specification will remain an open question until the fundamental processes and flows are understood.
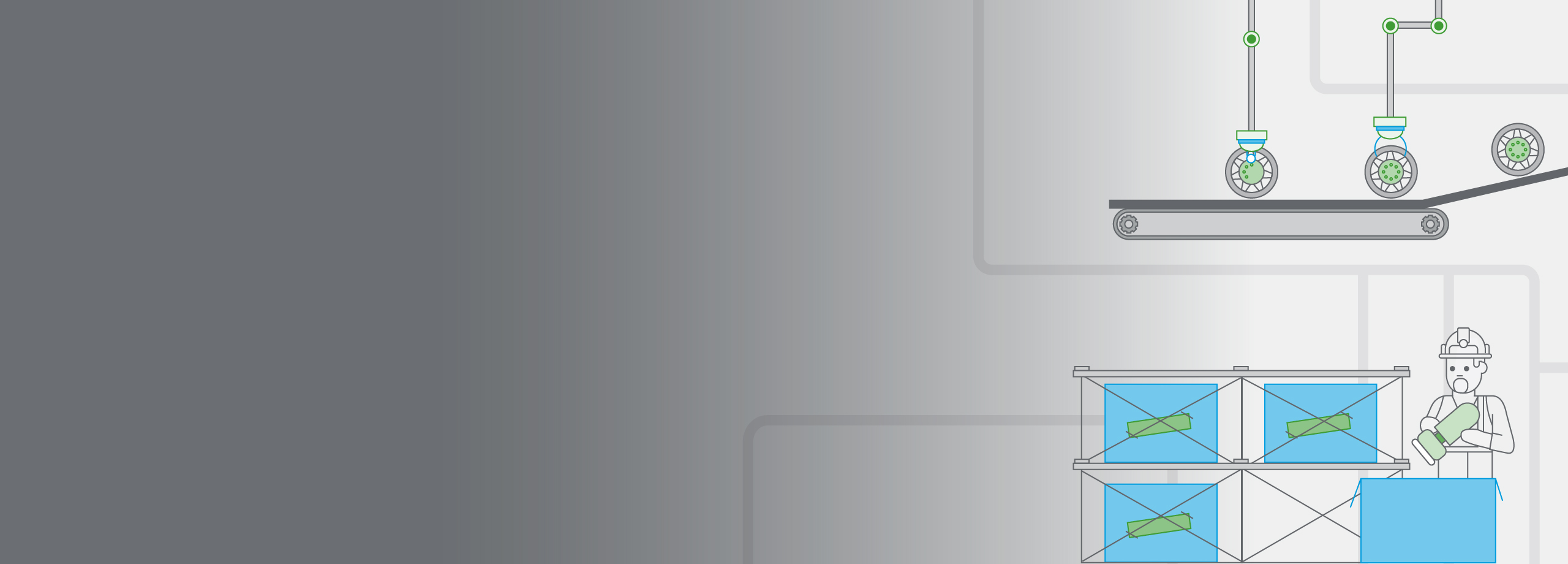
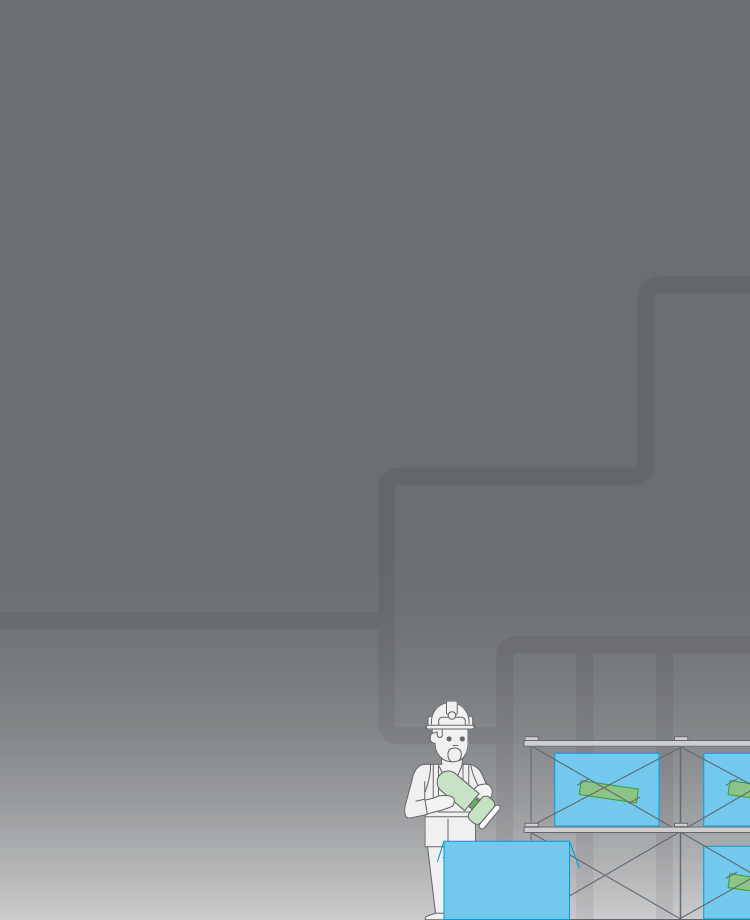